Blog
We share expert tips, industry insights, and the latest news in plumbing and pipe restoration. Stay informed and empowered with the knowledge to keep your plumbing systems running smoothly and efficiently.
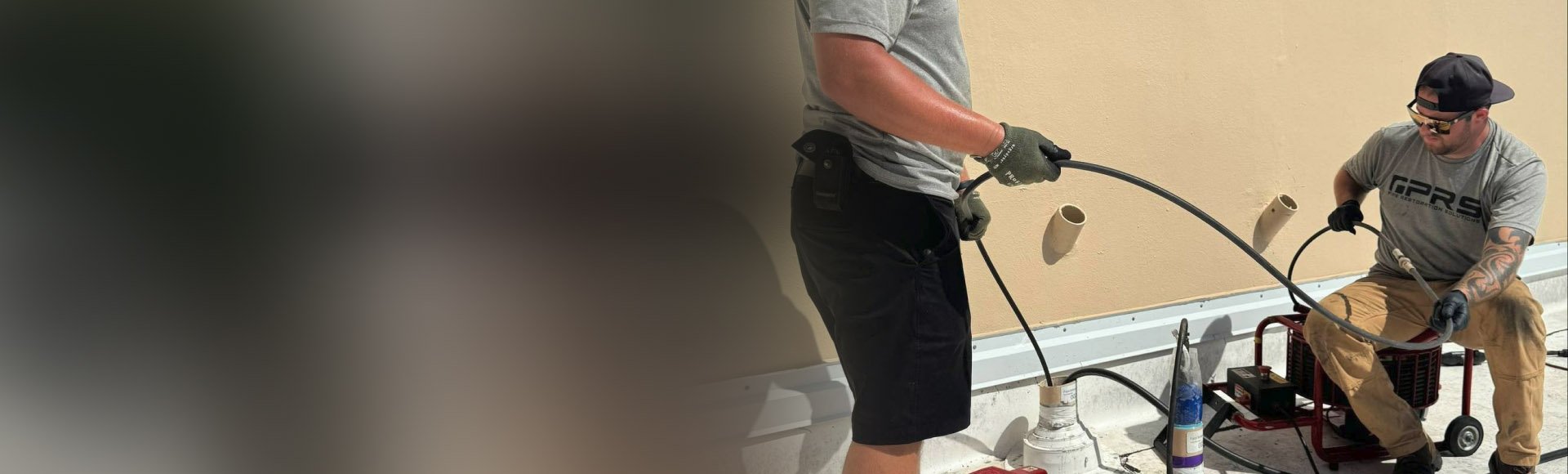
Innovations in Trenchless No-Dig Pipe Repair: The Latest Techniques
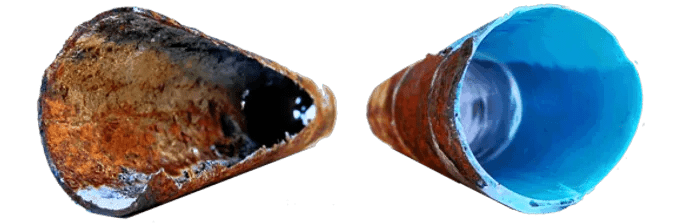
Cured-in-Place Pipe (CIPP) Lining
Cured-in-Place Pipe (CIPP) is one of the best trenchless pipe rehabilitation systems, offering a seamless and non-invasive approach to restoring pipes. This innovative technique introduces a resin-soaked liner into the compromised pipeline, which is then expanded to fit snugly against the pipe’s interior walls. As the resin hardens, it forms a new, corrosion-resistant lining that adheres tightly to the existing structure.
The choice of resin—be it epoxy, vinyl ester, or polyester—is dictated by the specific requirements of the job, including the type of pipe and the conditions it faces. The hardening of the liner, or curing, can be achieved through various methods such as hot water, steam, or ultraviolet light, each selected based on the optimal outcome for the material and environment.
CIPP lining’s adaptability makes it suitable for various pipe sizes and materials, from cast iron and clay to PVC and steel. Its application shines in situations where traditional excavation would cause significant disruption, such as in urban areas, beneath waterways, or around building foundations.
The process begins with meticulous pipeline cleaning, often involving high-pressure water or mechanical techniques, to ensure a strong bond between the liner and the pipe. The liner is then carefully inserted, typically by inversion, which utilizes water or air pressure to evert the liner into place. Following the curing phase, service connections are meticulously reinstated, often with the precision of robotic cutters, to bring the system back to full functionality.
Championed for its environmental sensitivity, swift completion time, and durability for the pipeline, CIPP lining is a robust solution that often surpasses the strength of the original pipe, promising extended service life and reliability.
Installation Process
Embarking on the CIPP installation journey, a detailed examination of the pipeline is paramount. This initial assessment, often conducted with closed-circuit television (CCTV) technology, provides a clear internal view of the pipe and aids in precise measurements, ensuring the liner’s perfect fit. Pipe Restoration Solutions is a leader in CIPP; we have offices in Florida and CA.
Following this inspection, the pipeline undergoes a rigorous cleaning regimen to eradicate obstructions such as roots and accumulated debris. This step is critical for the liner’s adhesion to the pipe walls, with hydro jetting and mechanical cutting tools being the instruments of choice for this task.
The next phase involves preparing the felt liner, which is saturated with a carefully selected resin tailored to the pipe’s condition and load requirements. The liner’s dimensions are meticulously determined from the initial CCTV footage to guarantee an exact fit. Depending on logistical and project-specific considerations, the impregnation process may take place either on-site or at a manufacturing facility.
Insertion of the liner into the pipeline follows, employing either the inversion method, which uses pressure to turn the liner inside out into the pipe, or the pull-in approach, where the liner is drawn into place with a winch. Once positioned, the curing phase commences, utilizing hot water, steam, or UV light, with the method chosen based on the system in use, site-specific conditions, and the type of resin.
Curing duration is contingent upon a variety of factors, including the diameter of the pipe and the curing method, ranging from several hours to a full day. Post-curing, the liner’s extremities are trimmed, and service connections are reopened, often with robotic precision. A conclusive CCTV inspection verifies the liner’s proper installation and the pipeline’s renewed structural integrity.
As we delve deeper into the benefits of this method in the Advantages of CIPP Lining section, it becomes clear why CIPP lining is a preferred choice for modern pipe repair.
Advantages of CIPP Lining
The trenchless CIPP lining technique stands out for its minimal disturbance to the environment, a feature that spares the landscape and existing structures from the chaos of traditional excavation. This eco-friendly approach not only conserves the surroundings but also slashes the costs and time associated with post-repair restorations.
A hallmark of CIPP lining is its exceptional durability. The liners, engineered for longevity, often exceed a 50-year lifespan, representing a prudent investment for the future. Their robustness against corrosion, wear, and the harsh subterranean chemical milieu translates into fewer maintenance demands as the years roll by.
Efficiency is another cornerstone of this method. Most CIPP lining projects wrap up within a single day, dramatically reducing the downtime for sewer systems and ensuring a swift resumption of normal operations for residents and businesses alike.
CIPP lining also brings hydraulic improvements to the table. The liner’s smooth interior surface can significantly boost the flow efficiency within pipes, outperforming the old, deteriorated pipe walls that often impede fluid movement.
The adaptability of CIPP technology is noteworthy, accommodating a spectrum of pipe diameters and materials, including clay, cast iron, PVC, and concrete. It adeptly addresses a variety of damages, from simple cracks to severe breakages and gaps.
Cost-effectiveness is the final piece of the puzzle. While the upfront costs may appear steep, the long-term savings from reduced ancillary damage, truncated project durations, and the extended lifespan of the repairs often tilt the scales in favor of CIPP lining over more conventional methods.
In essence, the CIPP lining process embodies a forward-thinking solution for no-dig pipe repair, consistently evolving to meet the complex needs of today’s infrastructure.
All our Locations can Help With Pipe Lining Your Cast Iron Pipes
Sarasota, FL
128 Sarasota Center Blvd
Sarasota, FL 34240
Phone: 800-652-7604
Irvine, CA
15510 Rockfield Blvd, Suite 100 C
Irvine, CA 92618
Phone: 800-652-7604
Naples, FL
196 16th Ave NE
Naples, FL 34120
Phone: 800-652-7604
Miami, FL
1388 NW 65th Terr
Plantation, FL 33313
Phone: 800-652-7604
Jacksonville, FL
14476 Duval Pl W
Jacksonville, FL 32218
Phone: 800-652-7604
Harbor City, CA
25029 S. Vermont Ave.
Harbor City, CA 90710
Phone: 800-652-7604
Pipe Bursting
Pipe bursting emerges as a robust solution for replacing pipes that have succumbed to age and wear, particularly those made from materials like clay, cast iron, and PVC. This method is the go-to choice when pipes are beyond the help of lining techniques such as CIPP.
At the heart of pipe bursting is a powerful bursting head that shatters the old pipe while a new one, usually composed of High-Density Polyethylene (HDPE), is drawn into place. This head, larger than the pipe it replaces, is driven through the existing line, breaking it apart and displacing the fragments into the surrounding soil. The new pipe trails the bursting head, occupying the same pathway to ensure a seamless replacement.
One significant advantage of pipe bursting is its capacity to enhance the pipeline by allowing the insertion of a new pipe with equal or greater diameter, all without substantial digging. This feature is particularly valuable in congested urban settings where surface disruptions can lead to considerable social and economic disturbances.
The speed and cost-efficiency of pipe bursting also stand out. The technique often outpaces traditional excavation methods, and when the reduced need for surface restoration is considered, it becomes an even more attractive option. Furthermore, the use of HDPE pipes, known for their resistance to corrosion and extended lifespan, adds to the long-term resilience of the pipeline infrastructure.
Pipe bursting is kinder to the environment than traditional trenching, as it preserves the ecological harmony in the vicinity of the pipeline.
With its combination of benefits, pipe bursting continues to gain prominence as a method for renewing outdated or compromised pipelines, and its capabilities are constantly being refined to accommodate an even broader array of pipe challenges.
Technique and Equipment
The pipe bursting method unfolds through a series of carefully orchestrated steps, relying on a suite of specialized machinery and a high level of technical know-how. At the heart of this operation is the bursting head, ingeniously crafted to shatter the old conduit while withstanding the surrounding earth’s resistance and the resulting debris.
Positioned within an access pit, a robust hydraulic or pneumatic pulling apparatus is the driving force that propels the bursting head through the existing pipeline. This machine is tethered to the head by a sturdy pulling rod or cable, which spans the entire length of the pipe segment being replaced.
Trailing the bursting head, a new pipe—typically composed of robust high-density polyethylene (HDPE)—is seamlessly heat-fused and drawn into position. This creates a continuous, joint-free pipeline that significantly reduces the risk of future leaks or invasive roots.
The operation may also employ an expander to widen the path for the new pipe and a retention device to secure the pipe in place during installation. Prior to commencing with pipe bursting, meticulous planning ensures that the chosen technique and tools are tailored to the specific project requirements, such as the existing pipe’s dimensions and material, soil characteristics, and proximity to other utilities. Strategic placement of entry and exit pits facilitates a smooth pipe bursting sequence.
Over time, the pipe bursting method has integrated technological enhancements, including remote monitoring and steering capabilities, which bolster control and precision. Despite these advancements, the core process remains anchored by the synergy between the bursting head and the pulling mechanism, ensuring the efficient renewal of aged or compromised pipelines.
Slip Lining and Lateral Rehabilitation
Slip lining stands as a venerable and uncomplicated trenchless technique for the restoration of pipelines. By inserting a new carrier pipe into the original pipeline, this method not only reinforces structural stability but also seals off potential leak points. The annular space between the host pipe and the liner is then filled with grout, solidifying the liner and distributing the load from the existing pipe.
The principles of slip lining are extended to lateral rehabilitation, addressing the repair needs of lateral pipes—those critical conduits linking individual properties to the main sewer. Due to their significance and often challenging access, trenchless technology has adapted to include specialized approaches for lateral repairs.
Among these is lateral lining, akin to CIPP lining, where a resin-imbued tube is introduced into the lateral pipe, hardened in place, and effectively creates a new pipe within the old one. Additionally, lateral reinstatement cutters—sophisticated robotic tools—navigate the relined lateral to precisely excise openings that align with the main sewer connections, thus ensuring uninterrupted service without the need for excavation.
Both slip lining and lateral rehabilitation represent non-intrusive alternatives to traditional repair methods, offering expedited completion times. These technologies enable the refurbishment of sewer laterals with minimal disruption to private property and public infrastructure, leading to considerable savings in restoration costs and a reduction in disturbances to communities and the environment.
Slip Lining Process
Embarking on the slip lining journey, the initial phase is a thorough pipeline evaluation using advanced closed-circuit television (CCTV) technology. This crucial step allows for an accurate assessment of the pipeline’s condition and informs the subsequent rehabilitation strategy. Following the inspection, the pipeline undergoes a meticulous cleaning process to eliminate any debris or blockages, paving the way for a seamless liner installation.
The liner selection is a tailored process, with high-density polyethylene (HDPE) pipes often chosen for their compatibility with the existing pipeline’s dimensions and contour. These liners are typically provided in segments and are expertly fused on-site to craft a continuous length tailored to the pipeline’s requirements.
The insertion of the liner marks a pivotal moment in the rehabilitation process. Depending on the specific circumstances and the tools at hand, the liner may be guided into place by either pushing or pulling, utilizing equipment such as winches or cranes to introduce the new pipe into the old infrastructure.
Grouting follows a step that cannot be overstated in its importance. By filling the annular space between the liner and the existing pipeline, grouting not only secures the liner in place but also ensures the structural integrity of the pipeline by transferring loads and filling any voids.
The slip liner’s ends are meticulously sealed to achieve a watertight repair. Depending on the project’s specific requirements, this can be accomplished using various materials, including rubber gaskets or additional grout.
In instances where service laterals have been obscured in the process, robotic cutting tools come into play. Operated remotely, these precision instruments make exact cuts to restore lateral connections.
The final step in the slip lining process is a comprehensive post-installation inspection. Utilizing CCTV or other advanced methods, this inspection verifies the repair’s integrity and confirms the proper reinstatement of lateral connections. Slip lining is celebrated for its efficiency and minimal disruption, offering a versatile solution for renewing pipelines across a spectrum of sizes and materials.
Lateral Repair Techniques
Addressing the critical segment that connects properties to the main sewer line, lateral repair techniques are employed to resolve issues like root intrusion, corrosion, or structural collapse due to environmental factors. Several trenchless methods stand out for their efficacy:
CIPP technology is not just for mainline fixes but is also a stalwart for lateral repairs. The process involves inserting a resin-saturated liner into the lateral pipe, which is then cured to form a robust, jointless new pipe within the existing one.
The Lateral Pull-in Place method is a nuanced variation of CIPP, where the liner is carefully pulled through the lateral and inflated to snugly fit against the pipe walls before the curing phase. This method’s precision is particularly beneficial for exact placement within lateral pipes.
When damage is localized, internal point repair is an economical and targeted approach. A segment of CIPP liner is applied directly to the damaged area, circumventing the need to reline the entire lateral.
Robotic systems offer precision for intricate lateral repairs. These advanced devices can navigate through laterals, conduct video inspections, excise obstructions, and install repair patches or full liners with remarkable accuracy.
Pipe coating with epoxy is another technique that fortifies the pipe’s interior, sealing leaks and warding off root intrusion and corrosion. The application is performed by a specialized device that ensures even distribution of the coating throughout the lateral.
Adapting the pipe bursting method for laterals involves using a head, either pneumatic or hydraulic, to break apart the old pipe, followed by pulling a new pipe, often made of HDPE, into place.
Selecting the most fitting lateral repair method is a nuanced decision, influenced by factors such as the extent of damage, lateral length, accessibility, and existing infrastructure. A careful analysis of these elements is essential to ensure the chosen technique delivers durability and cost efficiency.
Robotic Cutting and Repair
The advent of robotic cutting and repair technologies has revolutionized trenchless pipe rehabilitation. These advanced machines traverse pipelines’ inner workings, performing detailed inspections, excising blockages, and executing precise repairs—all with minimal disturbance to the ground above.
- Robotic Cutters: Equipped with high-resolution cameras and robust cutting implements, these robots excel in precision work. They deftly remove intrusive roots and concrete, crucial for restoring service connections post-CIPP lining by reinstating lateral connections and clearing obstructions.
- Robotic Repair Systems: Beyond cutting, these systems are adept at executing spot repairs. They employ patching techniques, where a small liner segment is applied to a compromised area, and resin injection methods, which seal fissures without the need for full lining.
- Packer Carriers: Integral to the repair process, robotic packer carriers precisely position patches and other repair materials. Their ability to inflate ensures a snug fit against the pipe’s interior, essential for an effective repair.
- Navigation and Control Technologies: These robots are outfitted with state-of-the-art sensors and tracking systems, including GPS, to navigate complex piping networks. This technology provides operators with immediate feedback, facilitating pinpoint accuracy in repairs.
- Resin Mixing and Application: Certain robotic units come with on-board systems to mix and apply resins directly within the pipeline. This capability guarantees the use of fresh materials, optimizing both the repair quality and the longevity of the coating.
Robotic cutting and repair technologies signify a quantum leap in capabilities, offering a level of precision and efficiency that manual methods simply cannot match. As these innovations continue to evolve, they are propelling the trenchless repair industry toward increasingly sophisticated and less disruptive solutions.
Robotic Capabilities
Robotic systems in pipe repair boast a comprehensive array of functionalities that enable them to address and rectify pipeline issues with unmatched precision and adaptability. These robots are a linchpin in the trenchless technology sector, bringing forth capabilities that streamline and refine the repair process:
- Precision Navigation: Robots are designed with sophisticated steering and propulsion systems, allowing them to deftly maneuver through intricate pipe layouts, circumvent bends, and smoothly pass by junctions and other structural features.
- In-Pipe Mobility: With a variety of locomotion mechanisms, such as wheeled or tracked movement, these robots adeptly navigate pipes of different diameters and materials, adapting to the unique challenges within each pipeline.
- Live Video Feed and Recording: High-definition cameras integrated into the robots provide operators with a live visual feed, crucial for the precise placement of the robot and for reviewing the completed work.
- Multifunctional Cutting Tools: Robots are equipped with an assortment of cutting heads tailored for various scenarios, enabling them to tackle obstructions ranging from organic roots to solidified concrete.
- Resinous Material Application: Robots can directly apply resinous materials to affected pipe areas, which are essential for structural repairs or for sealing joints and fissures.
- Automated Repair Processes: Some repair tasks, such as internal point repairs, can be automated, ensuring consistency and quality while reducing the potential for human error and enhancing overall safety.
- Telemetry and Diagnostics: These robotic systems provide comprehensive data on pipe conditions and the progress of repairs, including environmental factors like temperature and humidity that can influence the resin curing process.
- Environmental Adaptability: Constructed to endure harsh conditions within pipelines, these robots are waterproof and capable of functioning in environments with diverse pH levels and chemical compositions.
The capabilities of these robotic systems have significantly advanced trenchless repair methodologies, enhancing pipe rehabilitation’s efficiency, safety, and durability. As robotic technology advances, it sets new standards for precision and minimally invasive approaches in the industry.
Quality Control and Inspection
Ensuring the integrity of trenchless pipe repairs is paramount, and this is where quality control and inspection become indispensable. These processes validate the repair’s adherence to stringent standards, safeguarding both performance and durability.
Pre-Repair Inspection: Initially, a comprehensive evaluation of the pipe’s condition is conducted using state-of-the-art techniques such as closed-circuit television (CCTV) or laser scanning. This assessment is crucial for tailoring a repair plan addressing the specific issues.
During Repair Monitoring: The application of resin-based liners requires vigilant oversight. Monitoring encompasses verifying the resin mixture, maintaining optimal temperatures for curing, and confirming that the liner uniformly adheres to the pipe’s interior, free from imperfections that could compromise the repair.
Post-Repair Inspections: After the repair, a meticulous examination is carried out with advanced imaging technologies to ensure the liner’s proper installation and curing. This step checks for a seamless interior surface and the absence of any structural flaws that could impede flow or cause future issues.
Documentation: Comprehensive video and written reports are compiled to chronicle the pipe’s condition before and after the repair, serving as a testament to the work’s quality and fulfilling regulatory compliance or warranty requirements.
Diagnostic Testing: Finally, tests such as leak detection, pressure assessments, and flow measurements are performed to further affirm the repair’s success and functionality.
Through these rigorous quality control and inspection steps, the trenchless repair process maintains a high standard, providing a reliable feedback mechanism that not only ensures excellence in the current project but also drives the evolution of trenchless technologies.
Post-Repair Inspections
The culmination of the trenchless repair process is the post-repair inspection, a critical phase that confirms the repair’s success and compliance with the project’s specifications.
Visual Inspections: Utilizing CCTV cameras, specialists conduct a thorough visual examination of the repaired pipe, scrutinizing the liner for any signs of defects or improper adhesion.
Leakage Tests: Hydrostatic testing is often employed to fill the pipe with water at a predetermined pressure to check for leaks. In certain cases, air testing may also be utilized to ensure airtightness.
Liner Thickness and Density Checks: To verify structural soundness, ultrasonic devices measure the cured liner’s thickness, ensuring it aligns with the intended design parameters.
Lateral and Junction Inspections: Special attention is given to service laterals and junctions, where precise cuts in the liner are necessary. These areas are inspected to confirm they are clear and correctly executed.
Structural Assessment: Advanced techniques, such as laser profiling, provide a detailed map of the pipe’s interior surface, enabling the identification of any irregularities that could compromise the repair’s integrity.
Flow Measurement: Assessing the flow capacity post-repair is essential to ensure that the pipeline functions efficiently, maintaining or enhancing its ability to transport water or sewage.
Documentation: The inspection’s findings are meticulously documented, creating a permanent record that supports future maintenance, serves as evidence of the repair’s quality, and may be required by local authorities or clients.
Post-repair inspections are the final step in affirming that the trenchless repair methods have been executed flawlessly, ensuring that the pipeline meets the operational standards it was designed to achieve.
Choosing the Right Repair Method
The selection of an optimal trenchless repair technique is a multifaceted process that hinges on the careful consideration of various elements. This critical decision-making step ensures the repair’s effectiveness and longevity while also being mindful of budgetary considerations. Here are the essential factors to ponder when deciding on the most fitting trenchless repair approach:
- Pipe’s Current State: Assessing the condition of the pipe, including the severity of damage, dimensions, material composition, and its operational role, is paramount in influencing the repair method choice.
- Accessibility for Repairs: The pipe’s location and the practicality of reaching it to carry out the repair are vital. Different methods necessitate varying levels of access and operational space.
- Project Goals: The objectives of the repair, such as sealing leaks or reinforcing structural stability, will guide the selection of the repair strategy. Some methods are designed to provide structural reinforcement, while others are more suitable for sealing purposes.
- Environmental Considerations: The environment encircling the pipe, including soil characteristics, water table levels, and the vicinity to other infrastructure, can sway the selection of the repair technology.
- Regulatory Adherence: Ensuring that the repair method is in compliance with all pertinent regulations is essential. Certain methods might be mandated or favored by regulatory entities based on the specific context or environmental sensitivities.
- Financial and Temporal Constraints: The budget and the timeline allocated for the repair project can significantly influence the method chosen. Some options may offer rapid execution but at a higher cost, or the reverse may be true.
- Durability and Performance: The anticipated longevity of the repair and the performance requirements over time are crucial. The selected method should correspond with these expectations and any potential future modifications to the pipeline system.
- Disruption Mitigation: While trenchless methods aim to reduce disruption, some may still impact nearby activities or traffic flow. The degree of acceptable interference will factor into the method selection.
- Resource Availability: The presence of specialized machinery and the expertise of contractors to perform the repair are also determining factors. Certain methods may be impractical in some regions due to these limitations.
By meticulously appraising these considerations, stakeholders can pinpoint the most suitable trenchless repair method that addresses their project’s specific requirements, thus ensuring a successful and minimally invasive rehabilitation.
Evaluating Repair Options
The assessment of trenchless repair alternatives is a structured endeavor that involves a series of steps to guarantee the most compatible solution for a particular project. These steps aim to balance each method’s strengths and limitations against the unique demands of the repair job.
- In-depth Pipe Analysis: The process begins with a comprehensive inspection of the pipe’s condition, utilizing advanced technologies like CCTV to understand the extent and nature of the damage.
- Pipe Characteristics Review: Evaluating the pipe’s attributes, including its diameter, length, material, and installation depth, helps to ascertain which repair methods are feasible. This also encompasses the consideration of the type of effluent the pipe carries.
- Constraint Identification: Site access, proximity to other utilities, environmental regulations, and community impact are scrutinized to pinpoint potential limitations that could restrict the applicability of certain repair techniques.
- Cost-Benefit Comparison: A financial analysis is conducted to juxtapose each method’s immediate and long-term costs, considering factors such as labor, materials, ongoing maintenance, and the economic benefits of minimized operational disruptions.
- Performance Projections: The anticipated outcomes of each method, such as enhanced structural integrity, leak prevention, and improved flow capacity, are evaluated against the repair objectives to ensure they satisfy the technical specifications of the project.
- Expert Consultations: Collaboration with industry experts and engineers is crucial to cover all technical considerations. Their expertise can offer deep insights into the practicality and limitations of each repair method.
- Historical Project Analysis: Investigating case studies or similar past projects can provide practical knowledge. These historical accounts can illuminate the real-world effectiveness and durability of the repair methods.
- Environmental Impact Assessment: The sustainability of the repair methods and the materials used, as well as their overall environmental impact, should be assessed to ensure alignment with ecological objectives.
- Compliance with Standards: It is imperative that the chosen repair method conforms to local building codes and industry benchmarks, which are designed to protect public health, safety, and infrastructure integrity.
- Pilot Project Implementation: In some instances, executing pilot repairs can offer tangible evidence of a method’s appropriateness for the specific repair scenario at hand.
Through a comprehensive evaluation that weighs these diverse factors, decision-makers can confidently select a trenchless repair option that delivers an effective, cost-efficient, and minimally disruptive solution tailored to their pipeline challenges.
1. What is trenchless no-dig pipe repair?
Trenchless no-dig pipe repair is an advanced engineering solution that fixes underground pipes without the need for disruptive excavation. This technique is often quicker, less expensive, and environmentally friendly.
2. What are some latest techniques in trenchless no-dig pipe repair?
The latest innovations include Cured-In-Place Pipe (CIPP) lining, Pipe Bursting, and Slip Lining. All these techniques use specialized technologies to repair or replace underground pipes with minimum surface disruption.
3. How does Cured-In-Place Pipe (CIPP) lining work?
In CIPP lining, a resin-saturated felt tube is inserted into the damaged pipe and then inflated. The resin hardens, creating a pipe within a pipe, thus repairing the damaged section without digging or disruption.
4. What is the role of Pipe Bursting in trenchless no-dig pipe repair?
Pipe bursting involves breaking the existing, damaged pipe using a bursting head and simultaneously pulling a new pipe into place. This approach minimizes the impact on the surrounding land while effectively replacing faulty pipes.
5. How efficient is the Slip Lining technique?
Slip lining is a simple yet efficient method where a smaller, carrier pipe is inserted into the larger, host pipe. Grouting fills the gap between the two pipes, creating a new, secure pipeline.
6. What are the environmental benefits of trenchless no-dig pipe repair?
Trenchless no-dig pipe repair minimizes surface disruption, reducing soil erosion and the destruction of surrounding habitats. This method also significantly restricts the amount of waste produced than traditional methods.
Related Posts
- October 5th, 2023
- David “Rudy” Rudisill
- Drain Pipe Maintenance
5 Compelling Reasons To Descale Your Pipes
Five Compelling Reasons To Descale Your Pipes Hard water deposits can wreak havoc on your…
- May 23rd, 2024
- David “Rudy” Rudisill
- Drain Pipe Maintenance
Cast Iron Sewer Pipes History and Repair
Cast Iron Sewer Pipes Are Aging Cast iron sewer pipes, often overshadowed by modern materials…