Blog
We share expert tips, industry insights, and the latest news in plumbing and pipe restoration. Stay informed and empowered with the knowledge to keep your plumbing systems running smoothly and efficiently.
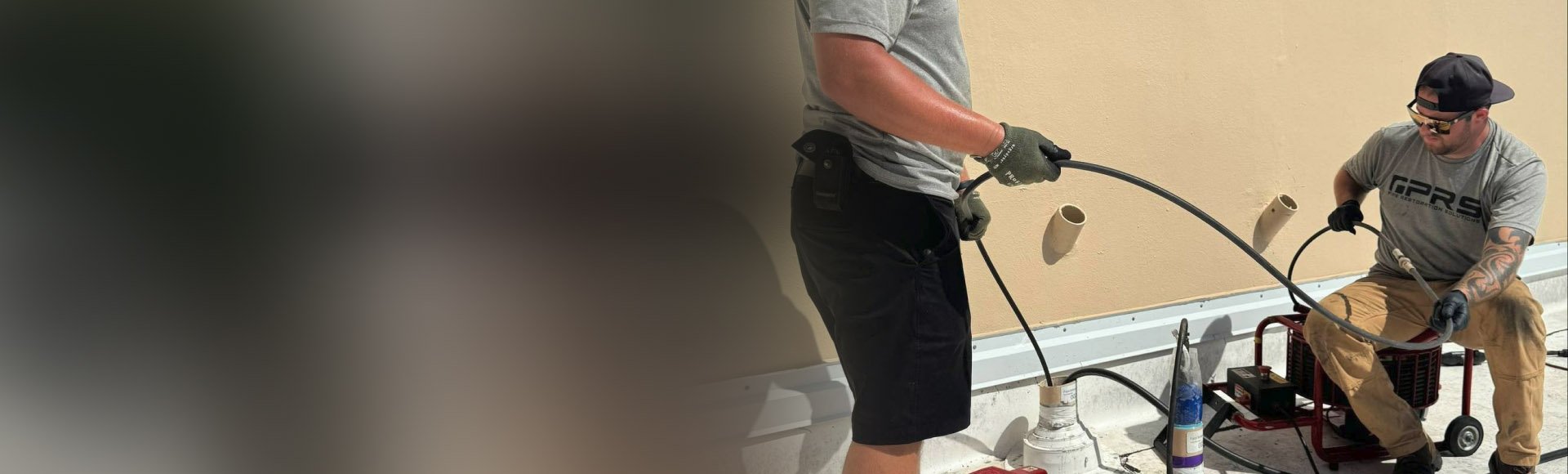
Cast Iron Sewer Pipes History and Repair
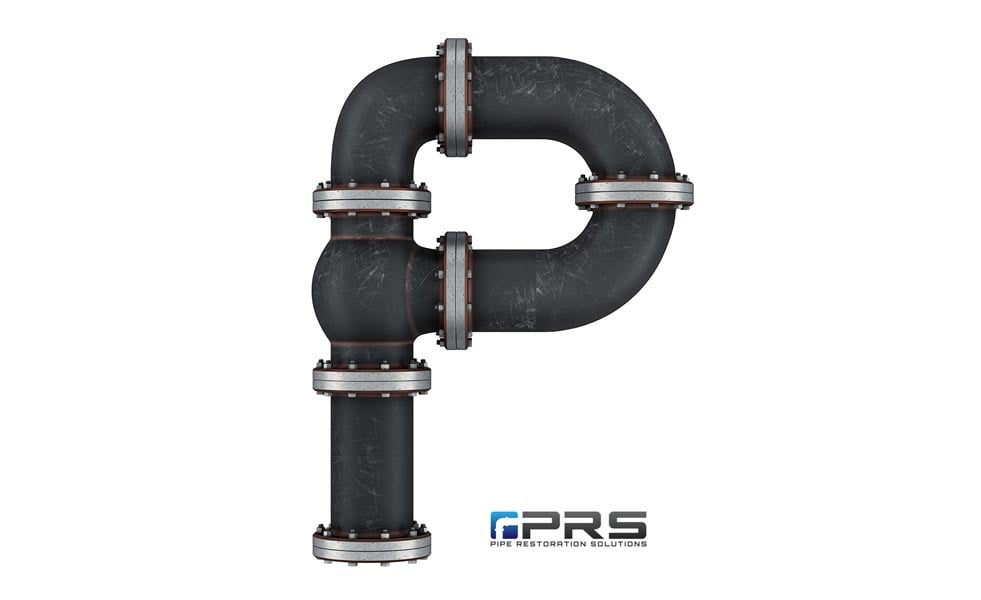
Cast Iron Sewer Pipes Are Aging
Cast iron sewer pipes, often overshadowed by modern materials like PVC and HDPE, hold a unique place in the infrastructure of our cities. Their unmatched durability and longevity have made them a foundational element of urban sanitation systems for generations. This enduring quality distinguishes cast iron pipes as a critical component in the plumbing world, offering a level of reliability that modern materials are still striving to match.
Key types of cast iron sewer pipes include the traditional bell and spigot pipes and the more modern no-hub cast iron pipes, each known for their robustness in different conditions. No-hub cast iron pipes, in particular, offer a simplified connection method that reduces the potential for leaks. Looking deeper, each kind of cast iron sewer pipe brings its own set of benefits, installation techniques, historical importance, and considerations for maintenance and repair.
The following sections will dive into these aspects in detail, providing a comprehensive understanding of why cast iron sewer pipes remain an invaluable asset to our plumbing systems. Despite the challenges they may face over time, such as corrosion, clogging, and cracking, the methods and technologies available for their repair have evolved, ensuring that cast iron sewer pipes can continue to serve communities for years to come.
What is the history of cast iron sewer pipes?
The journey of cast iron sewer pipes began in the early 17th century, marking a significant evolution in urban sanitation. Initially used in France, their adoption spread rapidly due to their superior durability and effectiveness in waste management compared to earlier materials like wood or clay. By the mid-19th century, cast iron pipes had become the backbone of sewer systems in Europe and America, revolutionizing public health by providing more reliable waste disposal solutions.
This historical shift not only improved urban living conditions but also laid the groundwork for modern plumbing systems, showcasing the enduring importance of cast iron sewer pipes in infrastructure development. Their ability to withstand the test of time, often serving for over a century, highlights their unparalleled contribution to the advancement of sewer systems worldwide.
Notable Implementations and Developments
- Paris, France: Among the first cities to implement cast iron pipes in the early 17th century, significantly improving the city’s waste management system and reducing the spread of diseases associated with poor sanitation.
- London, England: The construction of the London sewerage system in the mid-19th century, led by engineer Joseph Bazalgette, utilized cast iron pipes extensively. This project is credited with dramatically improving public health by effectively managing waste and reducing the incidence of cholera and other waterborne diseases.
- Philadelphia, USA: One of the first American cities to adopt cast iron sewer pipes, contributing to the development of a more sophisticated and sanitary urban infrastructure. The introduction of these pipes in the 19th century played a crucial role in controlling outbreaks of diseases such as yellow fever.
Impact on Public Health and Infrastructure
The adoption of cast iron sewer pipes marked a pivotal moment in urban development, directly impacting public health and the quality of urban life. By providing a durable and effective solution for waste management, these pipes helped mitigate the spread of diseases, leading to healthier populations and more livable cities. Furthermore, the reliability and longevity of cast iron contributed to the sustainability of urban infrastructure, reducing the need for frequent repairs and replacements.
Why are cast iron sewer pipes used?
Cast iron sewer pipes are chosen for two primary reasons: their exceptional durability against waste corrosion and their impressive longevity, often exceeding a century. This durability ensures that the pipes can handle a variety of waste without deteriorating quickly, making them a reliable choice for urban sewer systems. Additionally, their ability to last for over 100 years offers a cost-effective solution for municipalities, as it reduces the need for frequent replacements.
The combination of these attributes makes cast iron sewer pipes an enduring favorite in constructing and maintaining efficient, long-lasting sewer infrastructures.
Comparative Table: Cast Iron vs. Other Materials
Material | Durability Against Corrosion | Longevity | Cost-Effectiveness | Installation Complexity |
---|---|---|---|---|
Cast Iron | High | >100 years | Moderate | High |
PVC | Moderate | 50-70 years | High | Low |
HDPE | High | 50-100 years | Moderate | Moderate |
Clay | Low | 50-60 years | Low | High |
- Durability Against Corrosion: Cast iron’s robust composition allows it to withstand aggressive chemicals present in sewage better than PVC and clay, ensuring the pipes remain intact over extensive periods.
- Longevity: Cast iron pipes often surpass 100 years of service, outliving PVC, HDPE, and clay pipes, which presents a cost-effective solution for municipalities by reducing the need for frequent replacements.
- Cost-Effectiveness: While the initial installation cost of cast iron can be higher than PVC, its longevity and durability offer long-term savings. HDPE offers a balance between durability and cost, but cast iron remains superior in terms of lifespan.
- Installation Complexity: Cast iron installation is more complex and labor-intensive compared to PVC, which is lightweight and easy to handle. HDPE and clay require moderate to high effort for installation but do not match the longevity and durability benefits of cast iron.
Durability against waste corrosion
The durability of cast iron sewer pipes against waste corrosion stands out as a key advantage. Their robust composition allows them to withstand the aggressive chemicals present in sewage, ensuring the pipes remain intact over extensive periods. This resilience is essential for the continuous, efficient operation of sewer systems, safeguarding them against leaks or potential environmental hazards.
Longevity of over a century
The longevity of cast iron sewer pipes is unparalleled, often surpassing 100 years of service. This remarkable lifespan reduces the frequency of necessary replacements, presenting a cost-effective and sustainable choice for municipal sewer systems. Their enduring nature not only supports current infrastructure needs but also lays a foundation for future generations, embodying a legacy of reliability and efficiency in waste management.
What are common issues with cast iron sewer pipes?
Cast iron sewer pipes, despite their durability and longevity, are not immune to problems. Corrosion, clogging from buildup, and cracking due to ground movement or pressure changes are prevalent issues. These challenges can compromise the system’s integrity and environmental safety, restrict flow causing backups, or lead to severe damage and costly repairs.
Regular maintenance and timely repair are crucial to ensure the efficient operation of cast iron sewer systems.
Case Studies and Examples Table
Issue | Description | Real-World Example |
---|---|---|
Corrosion | Leads to leaks, compromising pipe structure and environmental safety. | In 2015, Flint, Michigan faced a public health crisis due to corroded iron water pipes leaking lead into the water supply. While not a sewer case, it underscores the critical nature of corrosion in iron piping systems. |
Clogging | Occurs when waste, grease, or other materials accumulate, hindering sewage flow. | New York City spends millions annually to clear fatbergs, large clogs of grease and waste, from its sewer system, including those involving older cast iron pipes. |
Cracking | Caused by ground movement, earthquakes, or construction vibrations, risking system functionality. | After the 1989 Loma Prieta earthquake, San Francisco had to repair and replace many cracked cast iron pipes that compromised the city’s sewer system. |
Corrosion leading to leaks
Corrosion significantly undermines the integrity of cast iron sewer pipes, leading to leaks. This degradation compromises the pipe’s structure and poses a risk to the environment by allowing untreated sewage to seep into the ground.
Clogging from buildup
Clogging is a common issue when waste, grease, or other materials accumulate within the pipes, hindering the smooth flow of sewage. This buildup can lead to serious backups and overflows, requiring immediate action to prevent sanitation and health issues.
Cracking due to ground movement
Cracking can occur in cast iron pipes due to various forms of ground movement, such as natural settling, earthquakes, or construction vibrations. These cracks jeopardize the sewer system’s functionality and may demand significant repair efforts or even full pipe replacement to ensure continued operation.
How can you identify problems with cast iron sewer pipes?
Identifying issues with cast iron sewer pipes involves a few key strategies. Visual inspection can reveal signs of rust and cracks, indicating corrosion or structural damage. Camera inspection, a more advanced technique, allows for a detailed view inside the pipes to identify clogs, cracks, or other anomalies.
Listening for unusual sounds, such as gurgling or dripping, can also hint at potential problems. Finally, monitoring water quality and pressure changes can indicate issues within the sewer system. These methods combined offer a comprehensive approach to detecting and addressing problems early, ensuring the longevity and efficiency of cast iron sewer pipes.
Inspection Frequency and Signs of Worsening Problems
- Inspection Frequency: For residential properties, it is recommended that visual inspections be conducted annually and camera inspections every 3 to 5 years. However, due to higher usage rates, more frequent inspections may be necessary for commercial or industrial properties.
- Signs of Worsening Problems: Increasing frequency of blockages, visible rust and cracks becoming more extensive, and persistent foul odors can indicate that problems are worsening. Additionally, a noticeable decline in water quality or pressure could signify a developing issue within the sewer system.
All our Locations can Help With Pipe Lining Your Cast Iron Pipes
Sarasota, FL
128 Sarasota Center Blvd
Sarasota, FL 34240
Phone: 800-652-7604
Irvine, CA
15510 Rockfield Blvd, Suite 100 C
Irvine, CA 92618
Phone: 800-652-7604
Naples, FL
196 16th Ave NE
Naples, FL 34120
Phone: 800-652-7604
Miami, FL
1388 NW 65th Terr
Plantation, FL 33313
Phone: 800-652-7604
Jacksonville, FL
14476 Duval Pl W
Jacksonville, FL 32218
Phone: 800-652-7604
Harbor City, CA
25029 S. Vermont Ave.
Harbor City, CA 90710
Phone: 800-652-7604
Cost Considerations
- Average Costs of Inspections: The cost of a camera inspection can range from $100 to $800, depending on the length of the sewer line and the complexity of the inspection. Visual inspections, primarily conducted by homeowners or maintenance staff, have no direct cost but require time and attention to detail.
- Potential Cost Savings from Early Detection: Early detection of issues like corrosion, clogs, or cracks can prevent more severe problems, such as pipe bursts or extensive water damage, which can be significantly more costly to repair. For example, the cost of repairing a burst pipe or extensive water damage can easily exceed $5,000, not including potential increases in water bills due to leaks.
Incorporating these details provides a more comprehensive guide on identifying problems with cast iron sewer pipes, emphasizing the importance of regular inspections, recognizing signs of deteriorating conditions, and understanding the financial implications of maintenance decisions. This enhanced approach helps property owners make informed decisions about the care and maintenance of their sewer systems, potentially saving significant amounts of money and avoiding disruptions by addressing issues early.
What are the methods for repairing cast iron sewer pipes?
Several methods are available for repairing cast iron sewer pipes, each suited to different types of damage and repair needs. Traditional replacement by excavation, pipe lining with epoxy, and pipe bursting are the primary methods used today. These repair methods provide a range of options to address the common issues of corrosion, clogging, and cracking in cast iron sewer pipes, ensuring their longevity and functionality.
Repair Methods Table
Repair Method | Effectiveness | Average Lifespan Post-Repair | Cost | Technological Advancements |
---|---|---|---|---|
Traditional Replacement | High | 50-100 years | High | GPS and GIS for precise excavation planning |
Pipe Lining with Epoxy | Moderate-High | 30-50 years | Moderate | UV-cured liners for faster curing times |
Pipe Bursting | High | 50-100 years | Moderate-High | Trenchless technology reduces surface disruption |
Traditional replacement by excavation
Traditional replacement by excavation is the most direct approach to repairing cast iron sewer pipes, requiring the physical removal of the earth above the damaged section to access and replace it. Despite its effectiveness in addressing severe damage, this method can significantly disrupt the landscape and existing structures. Technological advancements like GPS and GIS have improved the precision of excavation planning, minimizing unnecessary disruption.
Pipe lining with epoxy
Pipe lining with epoxy presents a less invasive alternative, rejuvenating damaged pipes internally. By inserting a liner coated with epoxy resin into the existing pipe, it cures to form a durable, corrosion-resistant inner layer, effectively sealing off leaks and preventing further deterioration with minimal disruption. Recent advancements include UV-cured liners, which significantly reduce curing times and improve the efficiency of repairs.
Pipe bursting for larger sections
For extensive damage, pipe bursting offers a solution by replacing long sections of cast iron sewer pipes without extensive excavation. This technique breaks the old pipe while simultaneously pulling through a new one, minimizing surface disruption and efficiently renewing the sewer line. This method benefits from trenchless technology advancements, which reduce surface disruption and make the process more efficient.
What are the considerations for choosing a repair method?
According to the experts at Pipe Restoration Solutions, several key considerations come into play when selecting a repair method for cast iron sewer pipes. Cost comparison and budget constraints, property disruption and landscape impact, and longevity of repair and future maintenance needs are essential factors. These considerations guide property owners toward solutions that offer lasting benefits while minimizing the need for frequent interventions.
Balancing these considerations ensures the selection of an appropriate, effective repair method that aligns with both immediate and long-term infrastructure goals.
Decision-Making Table with Case Scenarios
Consideration | Description | Case Scenario |
---|---|---|
Cost Comparison and Budget Constraints | Evaluating the financial viability of repair options relative to available budgets. | A small municipality opts for pipe lining with epoxy due to limited budget, avoiding the higher costs associated with traditional excavation. |
Property Disruption and Landscape Impact | Assessing the potential impact on the surrounding landscape and structures. | A historic district chooses pipe bursting to replace a severely damaged sewer line, minimizing disruption to protected heritage sites. |
Longevity of Repair and Future Maintenance | Considering the durability of the repair and the likelihood of future maintenance requirements. | A coastal town with high groundwater levels selects traditional replacement for its ability to withstand environmental pressures, ensuring a longer-lasting solution despite the initial disruption and cost. |
Cost comparison and budget constraints
Cost comparison and budget constraints are critical in deciding on a repair approach for cast iron sewer pipes. The price range between methods, such as the more expensive traditional excavation versus the cost-efficient trenchless techniques like epoxy lining or pipe bursting, necessitates a thorough financial assessment. Homeowners and property managers must align repair choices with available budgets, ensuring an economically viable solution without compromising on quality.
Property disruption and landscape impact
Property disruption and landscape impact are significant factors in the selection process. Traditional excavation methods can lead to considerable disturbance, affecting landscapes and hardscapes, and potentially requiring costly restorations. Trenchless technologies offer a less intrusive alternative, minimizing damage to the property’s exterior and reducing the need for subsequent landscape rehabilitation efforts.
Longevity of repair and future maintenance
The longevity of repair and future maintenance considerations are paramount for a lasting solution. While some repairs might offer a quick fix, they could lead to more frequent maintenance issues. Options like complete pipe replacement, despite their initial higher costs and greater invasiveness, may afford longer-term benefits with reduced maintenance demands, ensuring a durable and reliable sewer system for the future.
What are the future alternatives to cast iron sewer pipes?
Looking ahead, the future of sewer infrastructure is moving towards materials like PVC pipes and HDPE pipes as alternatives to cast iron. PVC pipes stand out for their flexibility and cost-effectiveness, making them a popular choice for new installations and repairs alike. They are lightweight, easy to install, and resistant to corrosion, addressing some of the main challenges associated with cast iron.
HDPE pipes, known for their environmental resistance, offer durability against harsh chemicals and varying temperatures, making them suitable for a wide range of applications. These alternatives not only promise longevity and reliability but also align with modern demands for sustainable and efficient sewer systems.
PVC pipes for flexibility and cost-effectiveness
PVC pipes have emerged as a leading choice for modern sewer systems, prized for their flexibility and cost-effectiveness. Their lightweight nature facilitates easier and quicker installation compared to heavier materials like cast iron. Additionally, PVC’s inherent resistance to corrosion extends the lifespan of sewer infrastructure, making it a financially savvy option for both new projects and repairs.
HDPE pipes for environmental resistance
HDPE pipes are distinguished by their exceptional environmental resistance, which makes them capable of enduring extreme temperatures and aggressive chemicals. This resilience makes HDPE an optimal material for sewer lines exposed to harsh environmental conditions. Offering both durability and versatility, HDPE pipes represent a forward-thinking solution to the challenges faced by traditional sewer pipe materials.
Related Posts
- July 31st, 2023
- David “Rudy” Rudisill
- Drain Pipe Maintenance
5 Common Toilet Issues and Complications
Everyone needs the toilet, but toilets can develop many issues. In some cases, this can…
- May 15th, 2024
- David “Rudy” Rudisill
- Drain Pipe Maintenance
Innovations in Trenchless No-Dig Pipe Repair: The Latest Techniques
Cured-in-Place Pipe (CIPP) Lining Cured-in-Place Pipe (CIPP) is one of the best trenchless pipe rehabilitation…